he goal of Holthinrichs Watches is to create such powerfully designed timepieces that people experience the emotional sensations that architecture can evoke through its spatial, structural, and artisanal complexity: architecture on the wrist.
"I want people to experience the emotional sensations that architecture can evoke through its spatial, structural, and artisanal complexity: architecture on the wrist. That is why our watches are named after architectural ornaments,” says Michiel Holthinrichs, founder of Holthinrichs Watches.
It is the brand’s deepest belief that this can only be achieved when the design philosophy flows through even the smallest details of the design: when all components work together without concessions, resulting in a true integral design. This has been Michiel’s dream from the start: the ultimate three-dimensional wrist sculpture.
With pride, they announce the outcome of that dream: Ornament Nouveau. A project they’ve been working on since 2017. It contains their first Dutch-made, in-house movement in an unprecedented sculptural design language.
The inspiration for Ornament Nouveau is drawn from Art Nouveau and Early Modernist architecture. Eugène Viollet-le-Duc, inventor of Art Nouveau, used modern technologies to slim down constructions and reshape the principles of architecture. This marked the beginning of steel structures and spectacular spatial design. Modern architecture was born.
The designer needs to know the properties of materials and the techniques to process them thoroughly in order to realise the best designs. All components and scales must follow a strict design language and concept to achieve a coherent whole. Every component must receive equal attention at all stages, from design to manufacturing and finishing. Each component must be exceptional on its own and, together, form a higher stage of beauty. Beauty is the result of a strict design doctrine, aesthetic talent, well-thought-out proportions, and exceptional craftsmanship.
Parts of the case are intentionally left unfinished to showcase the process of making as part of the design’s aesthetic. This aligns with the modernist concept of “Horlogerie Brut” (coined from Le Corbusier’s Béton Brut). The concept stands for heavy textural play, material honesty, natural patinas, and raw aesthetics directly derived from manufacturing processes, combined with contrasting refined manual finishing. Ornament Nouveau’s case is made of titanium, providing sufficient strength for the thin lines of the lugs and allowing for customisations with selective surfaces anodised in several colours.
Every aspect of Ornament Nouveau is designed to be an individual art piece and an integral part of the overall design.
1. A unique titanium 3D-printed case
The case stands out with its unique and innovative design, instantly recognisable by its exceptional double-curved surfaces that dynamically float from the lugs around the caseband. Its organically shaped lugs are inspired by both Art Nouveau and nature and are connected to the case’s main body in a spectacular way. Organic, openworked structures could only be achieved using the latest innovations in high-end 3D metal printing. Ornament Nouveau’s unprecedented design is intended to expand the possibilities of modern design in watchmaking, creating a three-dimensional sculpture that leaves viewers wondering how it was formed.
The extensive process of 3D printing is highly complex: first, the printing chamber is filled with uniformly sized titanium grade 5 particles. Layers of 50 μm are formed by a nozzle adding a binder to the powder. Forming all the layers of a single case takes up to 24 hours. Afterward, the object must be sintered at about 1300 degrees Celsius, dissolving the binder and fusing the metal to form the case. This process is delicate and error-sensitive, and each model must be carefully checked and measured to ensure it meets the required specifications.
Once passed through QC, the case still requires CNC milling for the fittings of the caseback, movement, and crystal. Only after this step can the complex sculpted shapes proceed to the final stage of selective manual finishing. Due to its intricate shapes, this final finishing can only be done by hand and takes a full week of filing and brushing to bring out the design’s beauty.
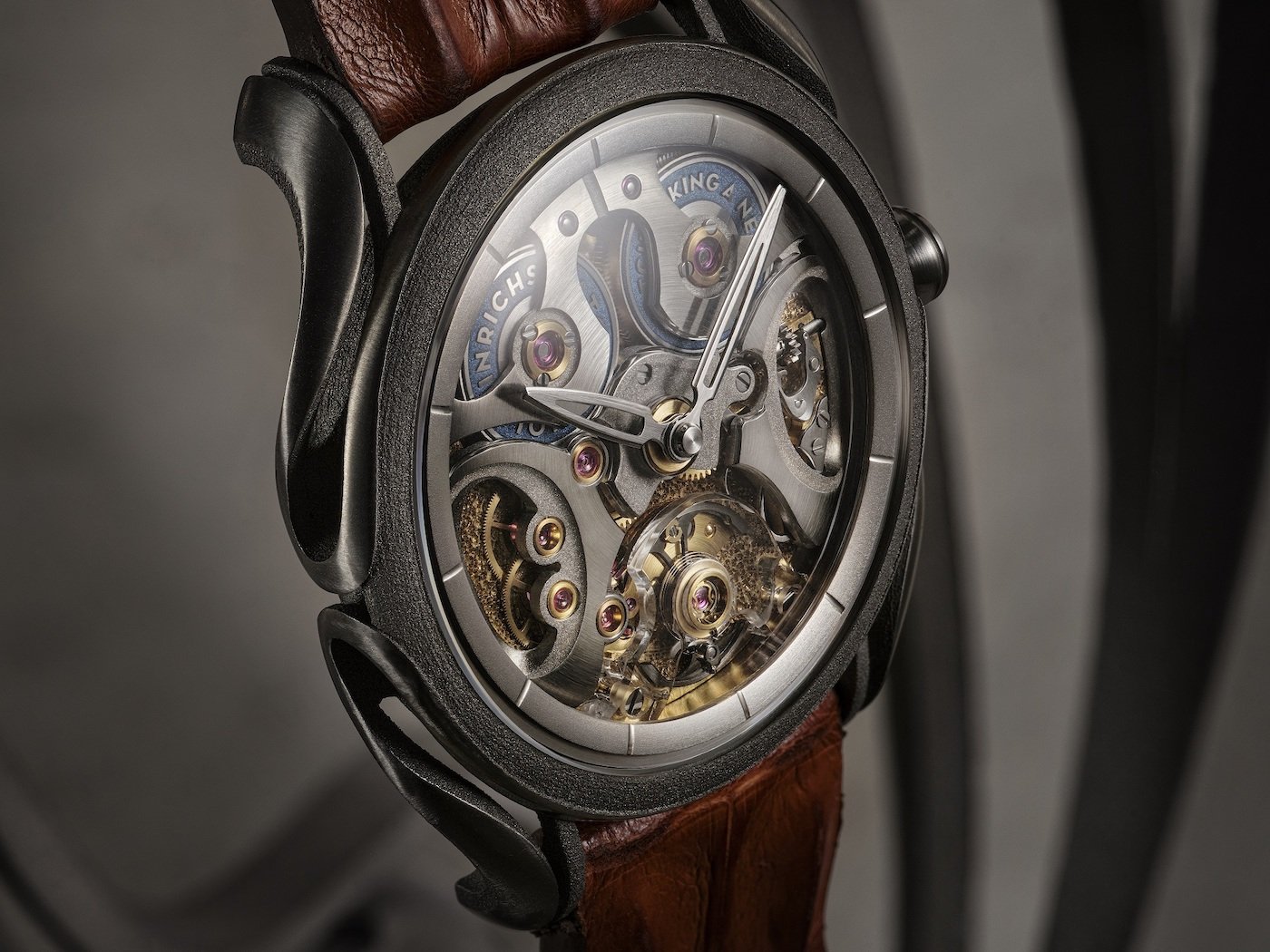
2. The first proprietary movement
Ornament Nouveau features the brand’s first, own movement, a spectacular and unprecedented sculptural design that fully reflects the overall design language of the watch. A dream come true, and the only way to realise their vision of fully integrated designs.
Creating this movement is a huge step for both the brand and the Netherlands. The calibre is developed, finished, and assembled in the Netherlands, with many components also manufactured locally. Crucial in this development is the relationship built over the years with a local precision manufacturer near Rotterdam, specialising in making highly specialised micro tools for medical purposes. After following the brand’s development, the manufacturer accepted the challenge of producing the ébauche parts. The goal is to build a Dutch manufacturing ecosystem for locally produced movements, largely independent of Swiss suppliers, contributing to the growth of the local watchmaking industry.
Though simple in function - displaying only hours and minutes - the movement is complex in execution. At just 4mm thick, it offers maximal three-dimensionality through complex machining and extensive manual finishing. The mainplate consists of a double concave shape, creating a strong optical three-dimensional effect. It is made of brass and available in four galvanic colours: 18K gold, 18K rose gold, white rhodium, or black rhodium. From the sides of the mainplate, organically shaped stainless steel bridges are cantilevered above the centre of the movement, each executed as miniature sculptures with multiple interacting three-dimensional surfaces and finished with contrasting textures and anglage for maximum visual depth.
The star of the movement is the in-house developed variable inertia balance wheel, a dynamically shaped openworked circle held in place by an exceptional three-dimensional glass bridge (called the “Holthinbridge”).
3. The novelty eclipse dial
At the centre of the movement, a specific cast-iron-like object bridge features a screwed-down nut, created to fix the unique dial developed for Ornament Nouveau. The dial, made of UV-sensitive photochromic material, is a novelty in the industry. It turns smoked black in UV light, protecting the oils in the skeleton movement from degradation and adding a playful aspect to the watch. Inside, one can see the beautiful sculptural movement, while outside in daylight, the watch transforms into a more classical timepiece, subduing the inner mechanics and emphasising the sculptural case.
4. The strap
The conception of Ornament Nouveau, with its three-dimensional shapes, made it clear that the model needed an exceptional strap to complete the concept. Nothing else other than nature could emphasise the brand’s commitment to organic design, so it was immediately clear to Michiel that the strap had to be crafted from the most beautiful part of the noble alligator: the tail. Its superb scales bring unprecedented depth and a sense of luxury. Though tough and difficult to work with, the brand selected three ateliers known for their beautiful craftsmanship to achieve one unparalleled result.
5. Presented in a unique sculpture
Uniquely for Ornament Nouveau the brand created a playful and light openworked art piece that serves as both an abri and a reflection of the delicate, complex design of Ornament Nouveau and its architectonic inspiration. The sculpture, composed of organic laces that float dynamically around the timepiece, was crafted from solid stainless steel using selective laser melting, another high-end 3D printing technology. It acts as both an object of art and a means to present Ornament Nouveau elegantly, covered by a protective, hand-blown glass dome. The sculpture can be commissioned to accompany the timepieces by both clients and retailers.
Michiel Holthinrichs (1990) launched Holthinrichs Watches in 2016. Holthinrichs Watches is a pioneer in the industry, combining state-of-the-art metal printing techniques, high-end artisanal hand-finishing, and a distinctive design language. The Ornament 1 was introduced in 2016 as the brand’s first modern take on the classic dress watch, featuring a pioneering 3D-printed case with unprecedented skeletonised shapes, Art Deco dial design, high-polished case, and slim dimensions.
Raw Ornament followed in 2018 with a brutalist design, where 3D-printed sculptural shapes and polished details were complemented by unfinished textures derived from the printing process. The “Horlogerie Brut” concept was introduced, extending to the movement and featuring a redeveloped bridge design, textural play, and extensive manual finishing. In 2022, the brand launched Liminality, a brutal model line proposing stages of visual destruction of the Ornament 1. In early 2023, the brand announced a full production stop of the Ornament 1 and Raw Ornament series to focus on new developments. Deconstructed was launched as the first watch, marking a new phase in the brand’s development.
This year, Holthinrichs Watches branched into two separate directions. The first branch, Holthinrichs Watches, focuses on building a strong brand reputation and design identity, taking a stand against today’s lack of design vision and quality. These watches form the brand’s Signature lines.
The second branch, Holthinrichs Haute Horlogerie, focuses on horological art, combining unconstrained creativity with high ambition to create three-dimensional wrist sculptures, develop an independent manufacturing ecosystem, and produce in-house movements with high-end manual finishing.
Holthinrichs Watches is based in the historical centre of Delft, The Netherlands.
TECHNICAL SPECIFICATIONS
Case:
- Material: 3D-printed titanium grade 5. Finishing according to our concept of “Horlogerie Brut”. RAW Textures with extensive selective manual finishing.
- Size: 39.5 (diameter excluding crown) x 47.2 mm (lug-to-lug)
- Thickness: 9.5 mm including double domed sapphire crystal.
- Water resistance: 5 ATM
Dial:
- The “Eclipse Dial’: a domed transparent dial that turns to smoke-black in UV light. The dial ring enclosing the transparent dial is made out of titanium and features a curved shape with milled and hand-polished hour indicators.
- Hands: Stainless steel sword shape hands, with large concave anglage on the blades and linear brushing on the top of the hands.
Movement:
- HW-M02 in-house developed manufacture hand-wound movement with double barrel in series
- Three-dimensional sculpted bridges, crafted out of stainless steel, all decorated with a rich play of frosting, brushing and handmade anglage. A double concave-shaped mainplate with frosting and diamond-tip hand-hammered textures. Jewels fitted in chatons. Screwed chatons on the barrels. Holthinrichs Swiss lever escapement with a free-sprung variable inertia balance wheel suspended in a 3D-machined glass bridge (the Holthinbridge). Integrated balance hack into the setting mechanism. All components, including the gears, screws and setting springs are decorated by hand in our atelier.
- Frequency: 21.600
- Jewels: 24
- Power reserve: Approximately 83h
- Functions: Hours, Minutes
Strap:
- Custom made Hornback alligator strap 20/16mm, with Holthinrichs 3D printed titanium buckle in brushed finish.
Availability:
- 100 pieces in total / maximum 20 timepieces per year at full capacity. Bespoke on request.
Price incl. VAT:
- Estimated starting at € 55,000 ex VAT in 3D printed steel / € 59,500 ex VAT in 3D printed titanium. Gold and precious metals upon request.