erhaps you remember Audrey Hepburn biting into a croissant as she glances up at the Tiffany & Co. clock in the opening scene of Breakfast at Tiffany’s? Ice-cream in hand, maybe you’ve wandered past the clock on Disneyworld’s Main Street? Or checked the time of the next departure on the giant-sized hands at Bang Sue Central Station in Bangkok? All these clocks were made by Electric Time Company, a family-run business in the state of Massachusetts which, over the years, has grown into the largest manufacturer of custom outdoor clocks in the United States.
Red maples and northern red oaks line country roads as, leaving the eight-lane highways behind, you drive deeper into New England towards the town of Medfield (population 12,000) and pull up outside Electric Time Company: 50,000 square feet (4,600 square metres) filled with hands large enough to slay a dragon and dials that would make a shield for Zeus.
Some 30 employees are hard at work. Engineers, craftspeople, lathe operators, CNC-machine operators, metalworkers, sculptors and painters, as well as sales and logistics staff. No sign of the white-coated watchmakers of the Swiss manufactories, bent over their workbench, a loupe clamped to their eye. The watchmakers in Medfield wear welding gloves and helmets as they shape metal into components. This is America where, the saying goes, everything is bigger, and Electric Time Company indeed makes clocks on a gigantic scale, without sacrificing any of the precision and attention to detail that comes with the horological terrain.
The company, which manufactures and repairs between 500 and 1,000 clocks a year, arose out of a revolution in timekeeping. Electric Time Company is an offshoot of Telechron, founded in 1912 in Ashland, some twenty miles from Medfield, by Henry E. Warren, the inventor of a self-starting synchronous motor. Patented in 1918, Warren’s motor was adapted to electric clocks that synchronised to the 60 cycles per second of the alternating current driving them. Millions of synchronous electric clocks were sold during the first half of the twentieth century, most of them marketed by General Electric and the Herschede clock company, making Warren − an electrical engineer trained at the Massachusetts Institute of Technology − the “father of electric time”.
-
- A Tiffany & Co. clock
American households couldn’t get enough of the “true time” of a Telechron clock. Jim Linz, author of Electrifying Time, writes that “in 1947, Warren Master Clocks regulated over 95 percent of the electric lines in the United States”. Thanks to Warren’s clocks, power stations were able to maintain alternating current at a uniform frequency of 60 Hz. The clocks’ popularity declined when the synchronous motor was superseded by the superior precision of quartz. General Electric sold the last Telechron plant in 1979 and the company closed down permanently in 1992. The remains of this technological adventure are a clock on display at the Smithsonian in Washington, Ashland’s high-school football team, “The Clockers”, and Electric Time Company.
Whereas Telechron made domestic clocks, ever since it was established in 1928, Electric Time Company has specialised in tower clocks, street clocks and bracket clocks for outdoor use. “We do things on a grand scale!” declares Thomas Erb, President, whose family of engineers bought the company in the mid-1960s. “The clock we made for Bang Sue station was so huge, our factory wasn’t big enough. We had to lift it out with a crane and finish it outside.”

The 20 ft (6.1m) diameter canister clock of Bangkok’s new Bang Sue Central Station, the largest railway station in Southeast Asia.
Electric Time Company says it can reproduce almost every type of model and style, the majority of which are driven by impulse movements. Its most challenging project to date? A reproduction of the Torre dell’Orologio in Padua for a private collector. Completed in 1427, this complex clock shows moon phases, days, months and the signs of the zodiac. Sometimes, difficulties are related not to the clock itself but the environment it is designed for. This was the case for a clock built for an automotive centre in Ottawa, where North American car manufacturers carry out cold-weather testing.
“Temperatures often fall below 30 or 40 degrees [below 0°C]. We use special motors and bearings that are suited to these conditions, which we test in an environmentally controlled chamber,” Thomas Erb explains. Thanks to this technology, the company has installed clocks – around 10,000 in all since 1928 – on every continent including Antarctica, from Taipei to the UK, from a stadium in Soweto to a shopping mall in Sao Paulo.
“We receive a lot of enquiries from film studios wanting a reproduction historic clock for a set,” Thomas Erb continues. The company is renowned for its reproductions of early 1900s street clocks (or post clocks, as they are also known) and takes orders from towns and cities across the United States. “A lot of towns want a street clock in the Victorian style, which is popular right now. It gives a historic feel to the space and provides a focal point for residents.”
-
- A street clock in Lexington, Virginia
Life isn’t always easy for these street clocks, particularly when confronted with drivers more accustomed to checking the time on their smartphone than at the corner of the street. “We travel all over the country to repair street clocks that have been in a collision with cars. Once, in New York, a hot-dog vendor got into an argument with a building owner and slammed his cart into one of our clocks, shattering the post!”
Accidents aside, monumental clocks are a fast-growing market, not just in the United States but worldwide. “A clock creates a sense of community, of belonging to a place. There has always been a tradition to ‘meet me under the clock’ and that’s a phrase we’re hearing more and more.”
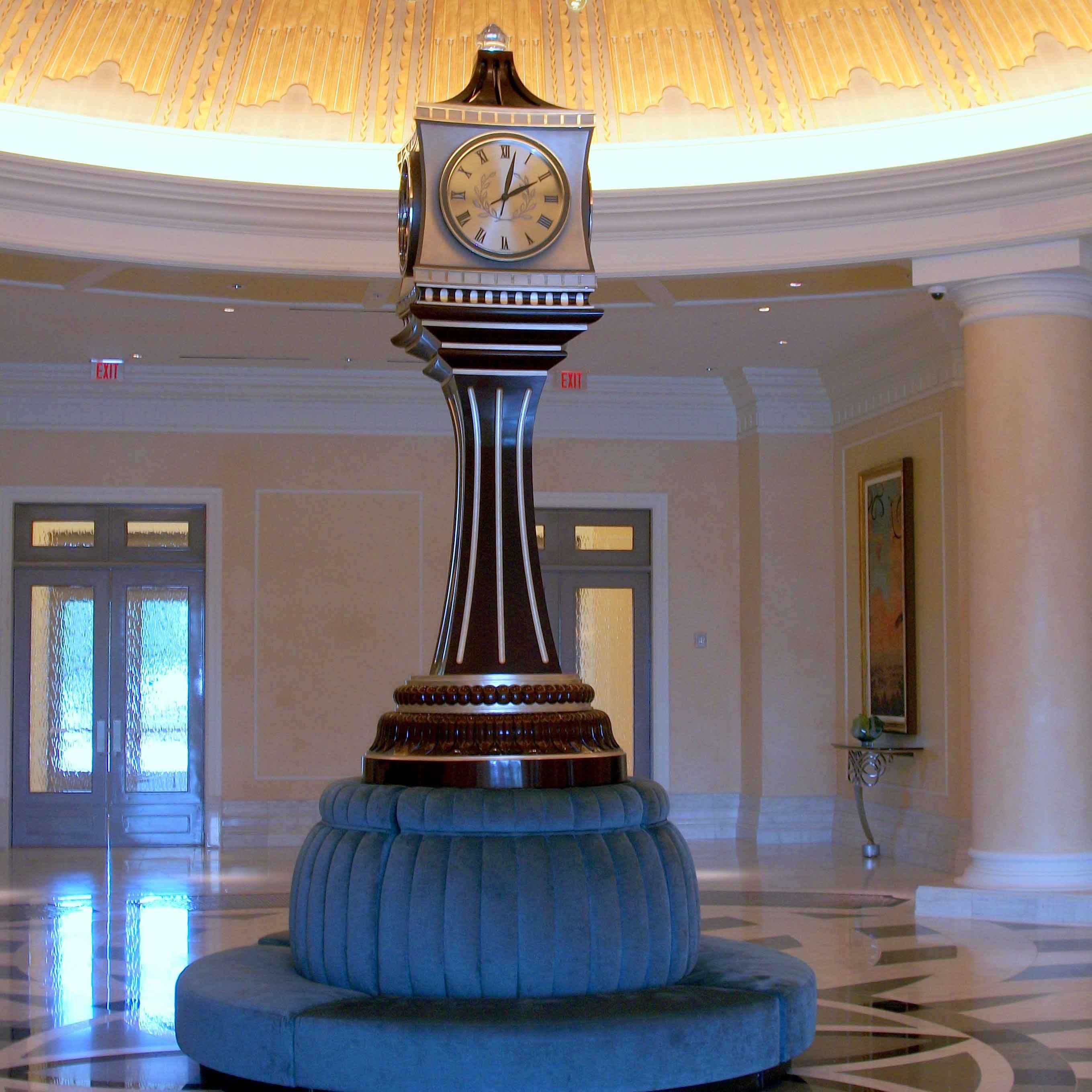